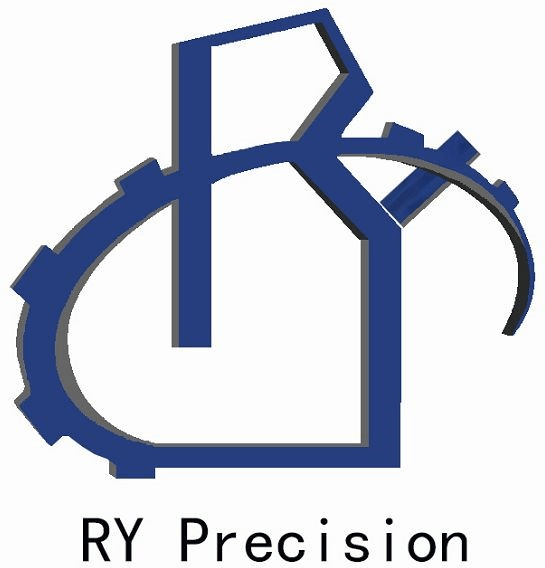
- Resources
- …
- Resources
- Resources
- …
- Resources
Case Studies
Our project managers at RyPrecision work with a range of product developers, product designers, entrepreneurs, and engineers from all over the world to help them make high-quality parts and products.
Have a look at some examples of projects we’ve worked on and see how they were made. Projects use a range of services including CNC machining, plastic injection molding, pressure die casting, vacuum casting, and more. If you’re working on a project with us and you would like our team to do a case study on your project, let us know!
Cormia Unisex Travel Razor Case Study
Services: CNC Machining, EDM Machining, Extrusion, Pressure Die Casting, Clear Coating.
Mold Material: H13 tool steel
Part Material: Aluminum ADC-12 and 6065
About the Project
Mario Cormier, the owner of Cormia Design of Canada, came up with the idea for this product. After trying many other kinds of razors, he found none of them were ideal for traveling. The Cormia travel razor is unisex, uses inexpensive replaceable twin blades, and is safe for air travel.
How The Parts Were Made
Pressure die casting molds were made from H13 tool steel using CNC machining and wire EDM. Several test castings were done to confirm the accuracy of the build and adjustments were made to the tool accordingly. The prototype samples were made from ADC12 aluminum alloy.
The cover needed to be made using a different process, so another tool was created for an aluminum extrusion using 6063 aluminum. 500 parts in various surface finishes were sent to the client for approval before he settled on a satin metal finish as the best option. Achieving this finish consistently required cleaning the parts and then clear-coating them to protect against oxidization.
Finally, all 500 parts were tested for conformity using Optical Emmission Spectrometry (OES) to check the validity of the raw materials and Faro laser scanning to confirm the dimensions of the complex topography of the cover plate.
Did you find this interesting? Read about some other projects we’ve worked on and the processes involved.
Let’s Start A New Project
Contact Us
Monday - Friday 9:00 AM - 5:00 PM
+86 18148951366
contact@